Stainless steel is renowned for its durability, clean appearance, and resistance to corrosion. However, to elevate its corrosion resistance and surface cleanliness—especially in industries like food processing and medical equipment manufacturing—the passivation process of stainless steel is essential. But what exactly does this process involve, and why is it so critical in high-purity applications?
This in-depth guide decodes the passivation stainless steel process, step-by-step, explaining its core principles, industry applications, process parameters, and how it integrates with broader stainless steel processing techniques.
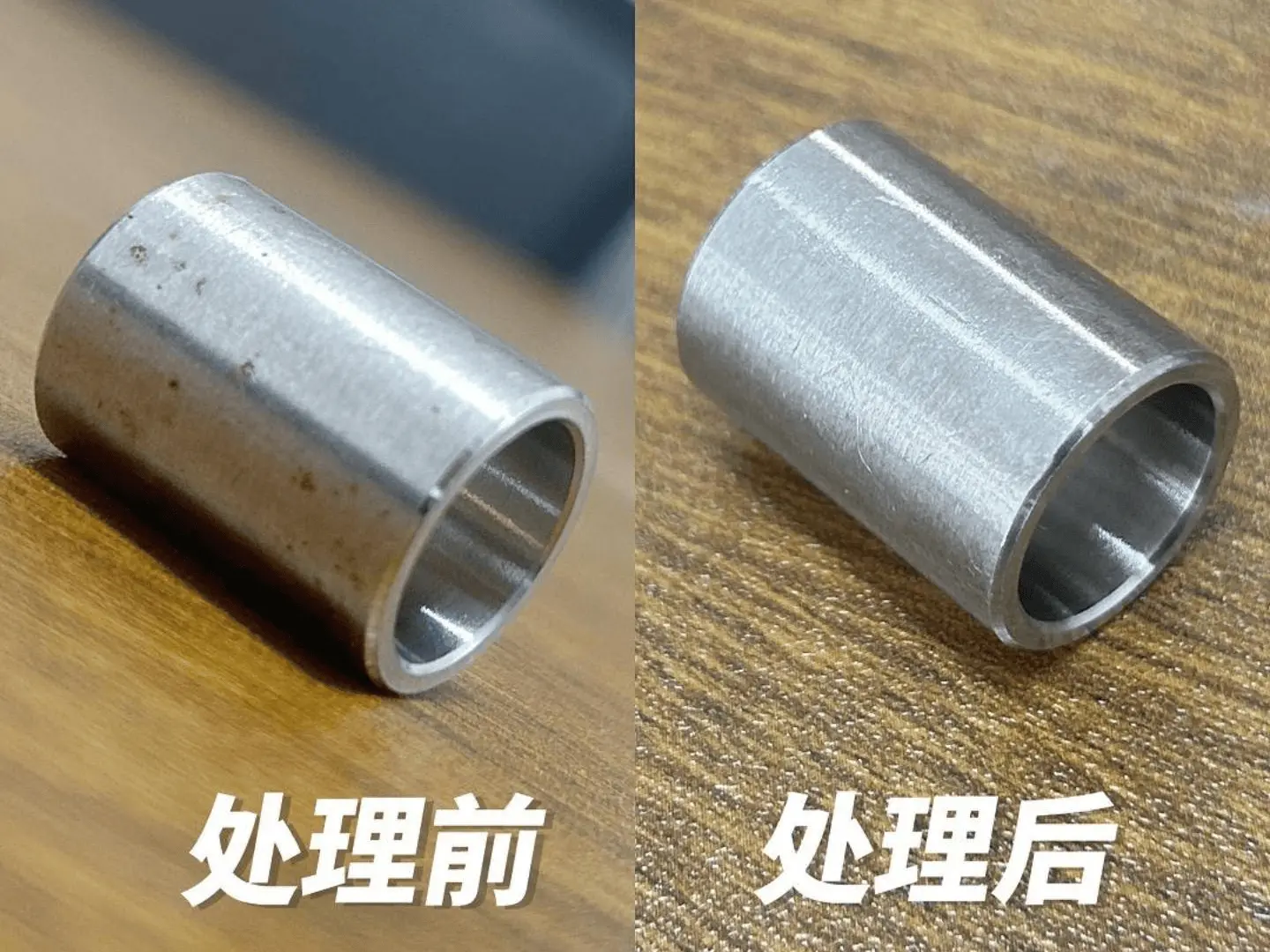
What Does Passivation Process Of Stainless Steel Do?
The passivation process of stainless steel refers to a chemical treatment that enhances the natural corrosion resistance of stainless steel by removing surface contaminants and promoting the formation of a thin, dense, and stable chromium oxide (Cr₂O₃) film. This film acts as a protective barrier, shielding the metal from environmental degradation and extending its service life by 10 to 30 times.
For example, passivated 304 stainless steel can withstand salt spray exposure for over 600 hours—compared to only 48 hours without treatment—making it vital for stainless steel food processing equipment, surgical instruments, and chemical process piping.
Passivation Process of Stainless Steel: Step-by-Step Breakdown
Following ASTM A967 and ASTM B912 standards, the passivation stainless steel process typically includes the following stages:
1. Pre-Cleaning / Alkaline Degreasing
- Objective: Remove cutting oils, lubricants, and contaminants.
- Method: Ultrasonic cleaning with alkaline degreaser (pH 10–12) at 60°C.
- Why it matters: Contaminants can block acid access and prevent oxide film formation.
2. Acid Pickling Activation
- Solution: 20% nitric acid + 3% hydrofluoric acid.
- Time: 20–30 minutes.
- Purpose: Dissolves free iron and sulfides, exposing a chromium-rich surface.
3. Chemical Passivation
- Standard Bath: 25% nitric acid at 49°C for 30 minutes.
- Reaction: Promotes Cr₂O₃ layer formation, 2–5 nm thick, enhancing corrosion resistance.
4. Neutralization and Rinse
- Neutralizer: Sodium carbonate (pH 8.5–9.5).
- Process: Multiple rinses with deionized or circulating water.
- Goal: Eliminate residual acids and prevent secondary corrosion.
5. Drying
- Method: Hot air drying at 80°C + oil-free air blast.
- Result: Spot-free, clean stainless steel surface.
6. Quality Inspection
- Test: Copper sulfate test (30+ seconds without discoloration).
- Verification: Confirms integrity of the passive film.
Critical Control Parameters for Stainless Steel Passivation
To ensure optimal passivation results, precise control over several key variables is required:
- Temperature Sensitivity: Every 10°C increase in nitric acid temperature doubles the reaction speed. Maintain ±2°C stability.
- Material Adaptation:
- 304/316 Stainless Steel: Best suited for standard nitric passivation.
- 420 Martensitic Stainless Steel: Requires annealing before passivation.
- Welded Areas: Post-weld electropolishing (12V, 3 mins) is necessary to remove chromium-depleted zones.
Synergy With Other Stainless Steel Processes
The passivation process does not work in isolation—it integrates seamlessly with other stainless steel manufacturing processes to achieve superior performance and compliance in critical applications.
1. Complete Stainless Steel Production Line
AOD Refining → Hot/Cold Rolling → Annealing (1050°C) → CNC Machining → Electropolishing → Passivation
- AOD Process: Reduces carbon to <0.03%, enhancing corrosion resistance.
- Electropolishing: Phosphoric-sulfuric acid system reduces surface roughness from Ra1.6μm to Ra0.2μm.
2. Food Processing Equipment Standards
- Requirements: FDA 21 CFR 175.300 compliance, chromium leach rate <0.5μg/cm².
- Design Considerations: Smooth transitions (R>3mm) to prevent microbial entrapment on stainless steel meat processing tables.
3. Heat Treatment Compatibility (420 Stainless Steel)
- Hardening: Vacuum quenching at 980°C followed by oil cooling.
- Tempering: 300°C for 2 hours, achieving HRC 50–55.
- Passivation: Citric acid solution preferred to reduce hydrogen embrittlement risk.
Stainless Steel Passivation Testing & Quality Assurance
Test | Method | Passing Criteria |
---|---|---|
Cr₂O₃ Layer Thickness | XPS Spectroscopy | Cr₂O₃ ≥ 12% surface composition |
Corrosion Resistance | ASTM B117 Salt Spray | ≥600 hours without red rust (304 SS) |
Free Iron Detection | Potassium Ferricyanide Paper | No blue spots (Fe²⁺ < 0.1μg/cm²) |
Surface Resistivity | Four-point probe | ≥1×10⁶ Ω/cm² (anti-static applications) |
Application Case Studies
Food-Grade Stainless Steel Table
- Material: 316L stainless steel.
- Result: Withstood 3% NaCl immersion for 72 hours without pitting.
- Finish: Electropolished + passivated (Ra <0.4μm).
Stainless Steel Process Piping
- Sequence: Internal sandblasting (Sa2.5) → nitric acid passivation → PTFE coating.
- Rating: PN40, resistant across pH 1–14.
Medical Equipment
- Post-passivation: Gamma sterilization tested.
- Result: Oxide film maintained integrity, no breakdown.
Troubleshooting Common Issues
Q1: Why do rainbow streaks appear after passivation?
- Cause: Over-pickling causes oxide film thickness variation.
- Solution: Limit nitric acid concentration to ≤25%; soak ≤40 minutes.
Q2: Welded zones corrode faster—why?
- Explanation: Heat-affected zones are chromium-depleted.
- Fix: Use localized electropolishing (15A/dm²) to restore chromium levels.
Q3: Can black stainless steel be passivated?
- Yes, with caution.
- Method: Post-PVD treatment with organic acid blend (2% oxalic + 1% tartaric acid, pH 3.5).
Why Choose Great Light for Stainless Steel Passivation?
At Great Light, we provide comprehensive 5-axis CNC machining and post-processing services, ensuring top-quality passivation for all stainless steel grades.
✅ Key Advantages:
- Custom Parameters: Optimized for 304, 316, and 420 stainless steel.
- Real-Time Monitoring: pH and ORP sensors ensure ±5% process stability.
- Eco-Friendly Solutions: Ion-exchange acid recycling system achieves 90% recovery.
📞 Contact us today for FDA-compliant, ISO-certified stainless steel passivation services that meet your industry’s strictest standards!
Final Thoughts
The stainless steel passivation process is a critical final step in stainless steel manufacturing, especially for high-purity and corrosion-sensitive applications. From food processing tables and process piping to medical instruments, this procedure ensures lasting performance and compliance with stringent safety regulations.
With precision-driven techniques and process control, Great Light delivers unmatched expertise in both CNC machining and stainless steel surface finishing. Ready to elevate your components? Let us handle your entire stainless steel journey—from raw material to final passivated perfection.